当前位置:
天津 恒永兴金属材料销售
有限公司 >丽水当地产品News
铝合金型材管线管拒绝中间商
更新时间:2025-01-16 19:32:49 浏览次数:16 公司名称:天津 恒永兴金属材料销售 有限公司
以下是:铝合金型材管线管拒绝中间商的产品参数
产品参数 | |
---|---|
产品价格 | 电议 |
发货期限 | 电议 |
供货总量 | 电议 |
运费说明 | 电议 |
品牌 | 恒永兴 |
规格 | 齐全 |
价格 | 电议 |
以下是:铝合金型材管线管拒绝中间商的图文视频
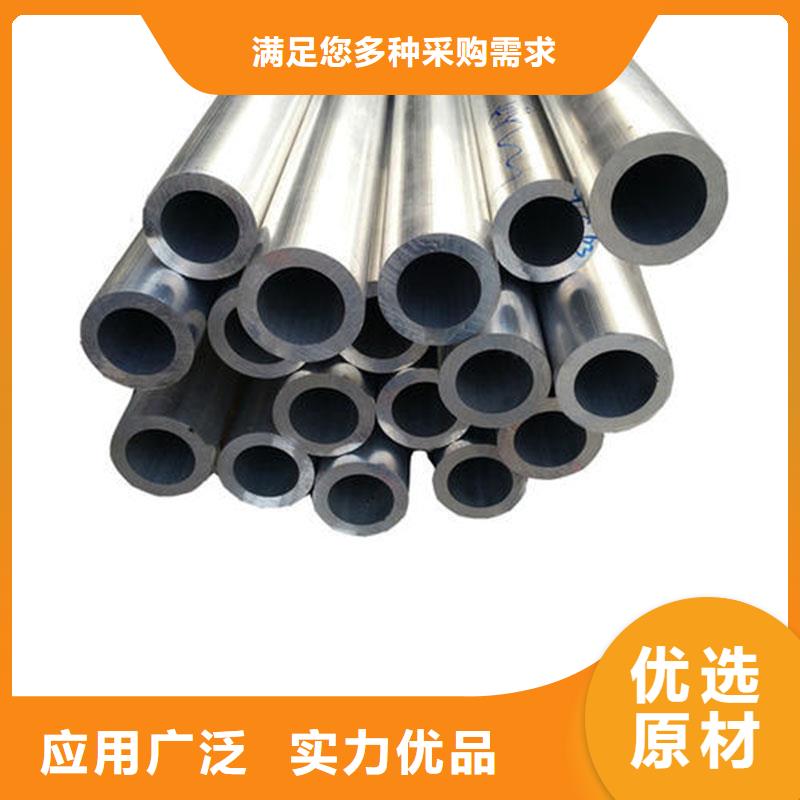

铝合金型材管线管拒绝中间商,恒永兴金属材料销售
有限公司为您提供铝合金型材管线管拒绝中间商的资讯,联系人:李经理,电话:022-86869388、18802286588,QQ:554918566,发货地:天津北辰区双街镇京津路西(北方实业发展有限公司内)发货到浙江省 丽水市 莲都区、青田县、缙云县、遂昌县、松阳县、云和县、庆元县、龙泉市。 浙江省,丽水市 1949年10月,设丽水专区;2000年7月19日,撤销行署建制,设丽水市。丽水市被誉为“浙江绿谷”,境内海拔1000米以上的山峰有3573座,龙泉市凤阳山黄茅尖海拔1929米,庆元县百山祖海拔1856.7米,分别为浙江省、第二高峰。丽水市是全国文明城市、生态示范区、生态保护与建设示范区、中国旅游城市、中国生态旅游城市、浙江省森林城市、浙江高质量发展建设共同富裕示范区首批试点之一、第二批“绿水青山就是金山银山”实践创新基地、第三批社会信用体系建设示范区;全市有多家A级景区,其中缙云仙都景区成为5A级旅游景区。
产品视频展示,助您洞悉铝合金型材管线管拒绝中间商产品的每一处细节。让购买决策变得轻松简单,为您带来更好的购物体验。
以下是:铝合金型材管线管拒绝中间商的图文介绍
恒永兴金属材料销售 有限公司拥有精良的加工,和检测设备,先进的 浙江丽水无缝钢管生产工艺,雄厚的技术力量,高素质的员工队伍,按照国际标准、标准、行业标准设计制造 浙江丽水无缝钢管产品,本着以质量求生存,以服务求发展的经营理念,竭诚为用户提供优质的 浙江丽水无缝钢管产品和优良的服务。
铝型材散热器生产工艺:首先贴膜不能直接贴在铬化层上,否则会影响膜的附着力;其次,贴膜后要及时喷涂不能停放时间过长,否则容易导致贴膜脱落,严重时还要重新贴膜;再次是撕膜时要控制流平时间,不能贴膜后马上撕膜,这样会对产品质量带来一定的影响;*后是两种颜色的喷涂顺序要根据具体情况确定,既要考虑到两次固化,又要考虑到遮盖效果。贴膜质量控制:散热器铝型材质量控制中贴膜质量很重要,若贴不好,会导致喷涂困难,如贴膜的张力不大、压紧程度要控制好;对形状复杂的部位要分开贴膜,贴膜后要检查贴膜是否贴牢。否则将会给喷涂带来麻烦。影响喷涂质量。公司生产的铝型材产品均由专业的技术人员严格把关,并拥有专业的生产设备,保证质量问题,客户可放心选购我厂产品。铝型材散热器的贴膜材质:首先要对贴膜材质合理选择,根据散热器铝型材产品的要求、表面处理方式,选择相应的贴膜,同是还要考虑贴膜上的胶对铝型材表面质量的影响。
缩孔是铝合金压铸件常见的内部缺陷,常出现在产品壁厚较大或者易形成热点的位置。一般来讲,只要缩孔不影响产品的使用性能,都以合格的方式来判定。然而,对于一些重要部位,如汽车发动机汽缸体的冷却水道孔或润滑油道孔,出现缩孔是不允许判定合格的。
某企业的一款铝合金制发动机曲轴箱,采用布勒28000kN冷室压铸机铸造,材质为ADC12合金,成分见表1。铸件毛坯质量为6.3 kg,后工序进行X射线探伤时发现第二个曲轴轴承孔油道出现缩孔,离油道约8 mm,存在较大的漏油风险。据统计,2017年该位置的缩孔报废率为5%,经过一系列的探索,成功地将废品率降低为0.2%。本课题从铝合金压铸件缩孔的形成机理[1-5]和铸造条件两方面出发,分析铸件产生缩孔的原因,寻求改善措施,以期为日后解决铝合金压铸件缩孔问题提供参考。一、铝合金压铸件缩孔形成机理及形态--缩孔形成机理:导致铝合金压铸件缩孔的原因较多,追溯其本源,主要是铝合金从液相向固相转变过程中铝液补缩不足而导致。常见的缩孔原因有:①模温梯度不合理,导致铝液局部收缩不一致。②铝液浇注量偏少,导致料饼薄,增压阶段补压不足。③模具存在热结或尖锐区域。④模具的内浇口宽度不够,面积较小,导致铸件过早凝固,增压阶段压力传递受阻、铝液无法补缩。⑤铸造压力设置过低,补缩效果较差。图1为铝合金铸件缩孔形成的示意图。铸件缩孔形态:缩孔是一种铝合金压铸件乃至铸件常见的内部缺陷,常出现在产品壁厚较大、模具尖角和模温温差较大等区域。图2为某款发动机曲轴箱缩孔形态,缩孔呈似椭圆状,距离轴承油道孔约10 mm,内壁粗糙,无光泽。缩孔区域铸件壁厚较大,约为22 mm;油道孔销子前端无冷却水,模温较高。汽车发动机曲轴的两大轴颈(主轴颈和连杆轴颈)工作载荷较大,磨损严重,工作时必须进行压力润滑。在此情况下,轴颈的油道孔附近若存在缩孔,将会严重影响润滑效果。二、缩孔相关对策:铝合金压铸件产生铸造缺陷的原因有产品本身的结构特征、模具设计得浇注系统及冷却系统设计不合理、工艺参数设计不合理等原因[1~4]。根据常见的铸造缺陷原因以及铝合金铸件缺陷处理流程,探索解决铝合金压铸件厚大部位缩孔的相应对策。前期分析及对策:铸件缩孔的前期分析从容易操作的工艺参数出发,通过现场测量及观察,测得模具内浇口厚度为4 mm,计算的内浇口速度为40 m/s,产品壁厚*薄处为4.6 mm;料饼厚度为25 mm;铸造压力为60MPa。由经验可知,模具设计符合产品的结构特征,模具浇注系统应该不存在增压阶段补缩不足的问题。但是,增压阶段的铝液补缩与料饼厚度和增压压力有直接的关系,合适的料饼厚度与铸造压力才能形成内部组 织致密的铸件,因此,可以怀疑缩孔是由铸造压力偏低和料饼偏薄而导致的。前期铸件缩孔的对策分为两个:①铸造压力由之前的65MPa提高至90MPa;②料饼厚度有原来的25 mm调整为30 mm。采用上述措施后,经过小批量专流验证,缩孔率由5%减低为4.8%,效果不明显,说明工艺参数不是引起铸件缩孔的主因。中期分析及对策:由于引起铸件缩孔的本质原因是铝液凝固时补缩不足而导致,而模具温度分布不均容易导致铝液凝固顺序不合理,从而补缩不足,因此,中期对策分析主要从确保合理的模具温度入手。由产品3D模型可知,铸件缩孔处壁厚为22.6mm,壁厚较大,容易引起较高的模具温度。铝液凝固时,壁厚较大铸件内部铝液由于温度较高,尚处于液相或者固液混合相,而此时内浇口进行补缩的通道可能已经凝固。这样,在增压阶段铸件无法进行铝液补缩,从而有形成缩孔的可能。为确保合适的模具温度,采用热成像仪测得脱模剂喷涂后模具*高温度为272℃(见图3),高于正常的模具喷涂后温度,其他区域模具温度及其分布整体正常。因此,需要降低缩孔处模温。另外,测得此处冷却水孔底部距离模具型腔表面距离较大为20 mm,因为较大的热传递距离会降低模具的冷却效果,所以需要对冷却水孔进行更改。为降低缩孔处模具温度,主要采取3个方法:①改善模具冷却系统。将缩孔附件的冷却水孔深度加深,由距模具表面20 mm变成12 mm,以此快速带走附近模具热量,降低模温;将所有模具冷却水管与水管统一编号,一一对应,防止模具保全时装错,影响冷却效果[5,6]。②降低浇注温度,由675℃变为645℃。③延长缩孔处模具喷涂时间,由2 s变成3 s。实施上述整改措施后,缩孔区域模具喷涂后温度大幅度降低,约为200℃,属于正常范围。缩孔率有4.8%降低到4%,说明此类措施对缩孔具有一定效果,但不能彻底解决此区域的缩孔问题。后期分析及对策:通过前面两次改善,基本保证压铸模具处于理论上的合理状态,即浇注系统设计合理、冷却系统布置合适,工艺参数设计*优。然而,铸件缩孔率仍有4%之多。铸件缩孔处壁厚为22.6 mm,远大于其他部位的壁厚,较大的壁厚可能引起铸件中心凝固时补缩不足,增压结束后此区域还没有完全凝固,继续收缩产生缩孔[7~10],模流分析见图4。因此,如何解决铸件缩孔处的补缩不足,也许才是问题的关键。一般来讲,铸件的补缩时通过料饼→浇道→内浇口→铸件这条路径进行的。由于铸件厚大部位后于内浇口凝固,切断了增压后期的补缩通道,因此无法补缩。
缩孔是铝合金压铸件常见的内部缺陷,常出现在产品壁厚较大或者易形成热点的位置。一般来讲,只要缩孔不影响产品的使用性能,都以合格的方式来判定。然而,对于一些重要部位,如汽车发动机汽缸体的冷却水道孔或润滑油道孔,出现缩孔是不允许判定合格的。
某企业的一款铝合金制发动机曲轴箱,采用布勒28000kN冷室压铸机铸造,材质为ADC12合金,成分见表1。铸件毛坯质量为6.3 kg,后工序进行X射线探伤时发现第二个曲轴轴承孔油道出现缩孔,离油道约8 mm,存在较大的漏油风险。据统计,2017年该位置的缩孔报废率为5%,经过一系列的探索,成功地将废品率降低为0.2%。本课题从铝合金压铸件缩孔的形成机理[1-5]和铸造条件两方面出发,分析铸件产生缩孔的原因,寻求改善措施,以期为日后解决铝合金压铸件缩孔问题提供参考。一、铝合金压铸件缩孔形成机理及形态--缩孔形成机理:导致铝合金压铸件缩孔的原因较多,追溯其本源,主要是铝合金从液相向固相转变过程中铝液补缩不足而导致。常见的缩孔原因有:①模温梯度不合理,导致铝液局部收缩不一致。②铝液浇注量偏少,导致料饼薄,增压阶段补压不足。③模具存在热结或尖锐区域。④模具的内浇口宽度不够,面积较小,导致铸件过早凝固,增压阶段压力传递受阻、铝液无法补缩。⑤铸造压力设置过低,补缩效果较差。图1为铝合金铸件缩孔形成的示意图。铸件缩孔形态:缩孔是一种铝合金压铸件乃至铸件常见的内部缺陷,常出现在产品壁厚较大、模具尖角和模温温差较大等区域。图2为某款发动机曲轴箱缩孔形态,缩孔呈似椭圆状,距离轴承油道孔约10 mm,内壁粗糙,无光泽。缩孔区域铸件壁厚较大,约为22 mm;油道孔销子前端无冷却水,模温较高。汽车发动机曲轴的两大轴颈(主轴颈和连杆轴颈)工作载荷较大,磨损严重,工作时必须进行压力润滑。在此情况下,轴颈的油道孔附近若存在缩孔,将会严重影响润滑效果。二、缩孔相关对策:铝合金压铸件产生铸造缺陷的原因有产品本身的结构特征、模具设计得浇注系统及冷却系统设计不合理、工艺参数设计不合理等原因[1~4]。根据常见的铸造缺陷原因以及铝合金铸件缺陷处理流程,探索解决铝合金压铸件厚大部位缩孔的相应对策。前期分析及对策:铸件缩孔的前期分析从容易操作的工艺参数出发,通过现场测量及观察,测得模具内浇口厚度为4 mm,计算的内浇口速度为40 m/s,产品壁厚*薄处为4.6 mm;料饼厚度为25 mm;铸造压力为60MPa。由经验可知,模具设计符合产品的结构特征,模具浇注系统应该不存在增压阶段补缩不足的问题。但是,增压阶段的铝液补缩与料饼厚度和增压压力有直接的关系,合适的料饼厚度与铸造压力才能形成内部组 织致密的铸件,因此,可以怀疑缩孔是由铸造压力偏低和料饼偏薄而导致的。前期铸件缩孔的对策分为两个:①铸造压力由之前的65MPa提高至90MPa;②料饼厚度有原来的25 mm调整为30 mm。采用上述措施后,经过小批量专流验证,缩孔率由5%减低为4.8%,效果不明显,说明工艺参数不是引起铸件缩孔的主因。中期分析及对策:由于引起铸件缩孔的本质原因是铝液凝固时补缩不足而导致,而模具温度分布不均容易导致铝液凝固顺序不合理,从而补缩不足,因此,中期对策分析主要从确保合理的模具温度入手。由产品3D模型可知,铸件缩孔处壁厚为22.6mm,壁厚较大,容易引起较高的模具温度。铝液凝固时,壁厚较大铸件内部铝液由于温度较高,尚处于液相或者固液混合相,而此时内浇口进行补缩的通道可能已经凝固。这样,在增压阶段铸件无法进行铝液补缩,从而有形成缩孔的可能。为确保合适的模具温度,采用热成像仪测得脱模剂喷涂后模具*高温度为272℃(见图3),高于正常的模具喷涂后温度,其他区域模具温度及其分布整体正常。因此,需要降低缩孔处模温。另外,测得此处冷却水孔底部距离模具型腔表面距离较大为20 mm,因为较大的热传递距离会降低模具的冷却效果,所以需要对冷却水孔进行更改。为降低缩孔处模具温度,主要采取3个方法:①改善模具冷却系统。将缩孔附件的冷却水孔深度加深,由距模具表面20 mm变成12 mm,以此快速带走附近模具热量,降低模温;将所有模具冷却水管与水管统一编号,一一对应,防止模具保全时装错,影响冷却效果[5,6]。②降低浇注温度,由675℃变为645℃。③延长缩孔处模具喷涂时间,由2 s变成3 s。实施上述整改措施后,缩孔区域模具喷涂后温度大幅度降低,约为200℃,属于正常范围。缩孔率有4.8%降低到4%,说明此类措施对缩孔具有一定效果,但不能彻底解决此区域的缩孔问题。后期分析及对策:通过前面两次改善,基本保证压铸模具处于理论上的合理状态,即浇注系统设计合理、冷却系统布置合适,工艺参数设计*优。然而,铸件缩孔率仍有4%之多。铸件缩孔处壁厚为22.6 mm,远大于其他部位的壁厚,较大的壁厚可能引起铸件中心凝固时补缩不足,增压结束后此区域还没有完全凝固,继续收缩产生缩孔[7~10],模流分析见图4。因此,如何解决铸件缩孔处的补缩不足,也许才是问题的关键。一般来讲,铸件的补缩时通过料饼→浇道→内浇口→铸件这条路径进行的。由于铸件厚大部位后于内浇口凝固,切断了增压后期的补缩通道,因此无法补缩。
铝板基材表面常见的四种处理--A对铝板基的技能需求:对制造PS版的铝板基较基本的技能需求是外表光滑平坦,无擦划伤、坑包、印痕、非金履压入、气孔、轧制条纹等表观缺点,厚薄一致,波涛度操控在1mm内,平直度小于2I;组 织细密均匀,无偏析、夹渣,内应力分由对称、均匀;粗糙度Ra值小于0.28,以确保电解砂目细密均匀。目前我国很多运用的板基材料为1050A、1060等。B碱洗:一般,由铝加工厂供给的铝板,其外表都带有一定量的油,油和氧化膜对砂目处置有影响,在PS版出产中常用热碱冲刷铝板进行外表处置。一般用碱液来去掉氧化膜和油。常用除油液的配比为:NaOH的质量钠等缓蚀剂及葡萄糖酸钠、脂肪酸聚氧乙烯醚类增溶、络合等外表活性剂。除油液的温度一般操控在55~60℃左右,除油的作用与溶液的温度有关。若温度太高,则造民对铝板基严重腐蚀,因此有必要操控温度。除油的时刻有必要通过仔细对比较终断定。由于,它与各种不一样出产线有关。卷筒出产线则与出产线的速度有关,以4m/min为例,除油时刻有必要这到20s,其作用才能处以确保。除油液有必要留意及时更新,由于在除油进程中会生成很多的皂化物、乳化物和铝盐,它们的存在影响除油作用,并阻止对铝板外表油污的皂化和乳化,当发现除油作用不强时,有必要及时更新。一般若通过碱泵进行循环时,除油液能坚持较长时刻,若不循环则更新时刻缩短。查看除油作用较简单的方法是用水。除油作用好的铝板外表水能均匀地附着涣散,若水倒上后,在铝板外表呈水珠状,则阐明除油作用欠好。除油的温度要常常留意,除油液的温度过低,则能够构成除油不完全。C酸洗:在出产工艺中,碱洗以后有一硝酸酸洗进程,其目的是去掉碱洗后的残留物质,中和剩余的碱液。硝酸溶液的质量浓度为5%~10%。配制时留意将硝酸小心肠倒入水中,充分混合。在酸洗进程中应常常留意溶液的浓度剖析,及时弥补。D粗化:粗化是为了构成具有需求粗糙度的砂目构造。粗化既可进步铝板基外表对水的亲和力,进步板基外表湿润量,避免版面上脏;一起粗化后的外表还可进步版同与感光剂的附着力,进而进步印版的耐印力。粗化后的砂目是由无数的凸峰和凹谷构成,不一样的砂目构造,对保水性感光层的附着力影响较大,并对PS版的运用带来较大影响。出产顶用外表粗糙度测试仪制作的砂目粗糙断面轮廓曲线的特征参数来表征。
在空分、液化天然气、石油化工、航天等领域,奥氏体不锈钢、铝合金有着日益广泛的应用。如何将这两种脾气、习性完全不对路子的材料结合在一起,困难可想而知.梳理国内外现状可以看出,目前钢铝连接,工程上主要采用两种方法:一种是将各自材料制成法兰,依靠螺栓联结在一起;另一种是钢铝焊接接头形成过渡。对于空分、液化天然气这种低温应用场合,螺栓联结可靠性远远不能满足工程需要,因而焊接过渡形式成为 方式。然而,钢铝焊接并非坦途一条。无论是钎焊、熔焊还是压焊,总是存在这样那样的问题难以克服。针对钢铝焊接存在的问题和难点,本研究组选择扩散焊工艺手段,以大尺寸、高可靠性钢铝转换接头为目标,深入开展相关工艺及性能评测工作并在以下几个方面获得关键性突破。1、了接头脆化问题:钢铝接头中Fe3Al型金属间化合物是接头脆化的根源。我们的工艺完全杜绝了金属间化合物的产生,从源头上了脆化的风险。而且,钢铝之间有显著的元素扩散,这是获得高结合强度界面的保证。2、高可靠性:考察钢铝扩散焊接头的拉伸性能可以发现,接头断在铝侧,说明钢-铝界面结合强度高,二者之间并非单纯的机械咬合。3、优异的耐高温性能:钢铝接头因为自身结构的特点,在两端与各自的材料焊接时,接头失效的风险很大。如钢铝爆炸焊接头结合面在施焊时温度一般控制在200℃×30min以下,法国T&C公司的钢铝接头hothopping工艺对温度更加敏感,结合面应控制在150℃以下使用。我们钢铝焊接接头经过400℃×20min的热处理后,接头试样同样断在铝合金母材位置。说明钢铝结合面性能并没有退化。目前,我们开发的焊接工艺适合各种尺寸的钢铝接头,而且接头尺寸越大,工艺优势越显著。
铝合金型材管线管拒绝中间商,恒永兴金属材料销售
有限公司为您提供铝合金型材管线管拒绝中间商产品案例,联系人:李经理,电话:022-86869388、18802286588,QQ:554918566,发货地:北辰区双街镇京津路西(北方实业发展有限公司内)。