当前位置:
天津 恒永兴金属材料销售
有限公司 >海南当地产品News
铝合金型材镀锌工角槽实体厂家大量现货
更新时间:2025-01-13 18:17:38 浏览次数:12 公司名称:天津 恒永兴金属材料销售 有限公司
以下是:铝合金型材镀锌工角槽实体厂家大量现货的产品参数
产品参数 | |
---|---|
产品价格 | 198 |
发货期限 | 电议 |
供货总量 | 电议 |
运费说明 | 电议 |
品牌 | 恒永兴 |
规格 | 齐全 |
价格 | 电议 |
以下是:铝合金型材镀锌工角槽实体厂家大量现货的图文视频
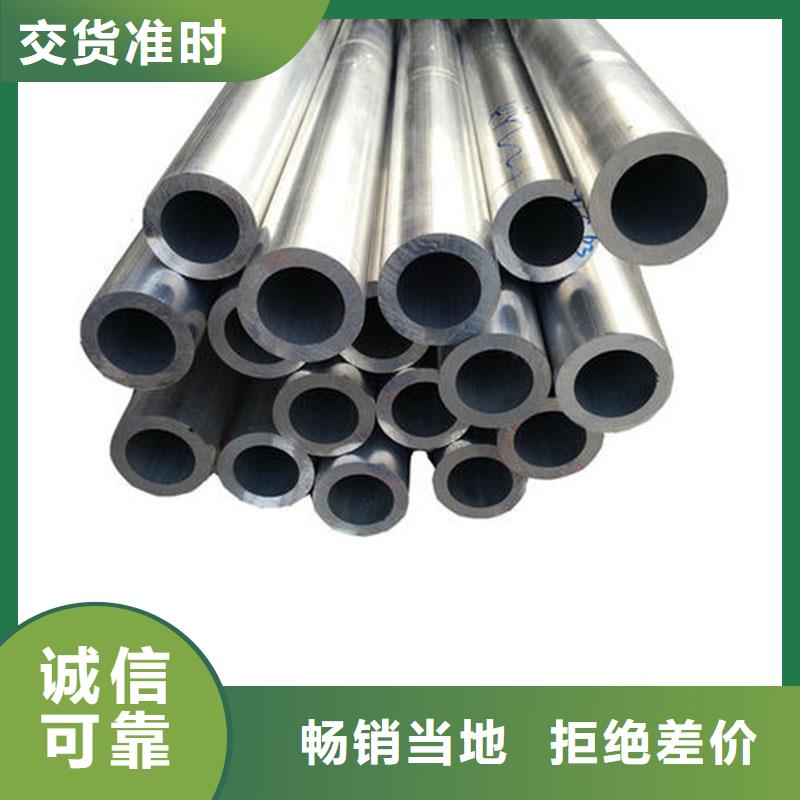

您是想要在海南省采购高质量的铝合金型材镀锌工角槽实体厂家大量现货产品吗?恒永兴金属材料销售
有限公司是您的不二之选!我们致力于提供品质保证、价格优惠的铝合金型材镀锌工角槽实体厂家大量现货产品,品种齐全,不断创新,致力于满足广大客户的多种需求,联系人:李经理-18802286588,QQ:554918566,地址:《天津北辰区双街镇京津路西(北方实业发展有限公司内)发货到海南省 海口市、三亚市》。 海南省 海南省是中国的经济特区、自由贸易试验区。历史上的火山喷发,在海南岛留下了许多死火山口;岛上温泉分布广泛,多数温泉矿化度低、温度高、水量大、水质佳,属于治疗性温泉。具有历史意义的古迹主要有为纪念李德裕等历史名臣而修建的五公祠,苏东坡居琼遗址东坡书院以及为纪念苏轼而修建的苏公祠,清代雷琼兵备道焦映汉所修建的琼台书院,明代名臣丘浚墓,明代大清官海瑞墓,相传受汉光武帝派遣率兵入海南的将军马援为拯救兵马而下令开凿的汉马伏波井,以及崖州古城、韦氏祠堂、文昌孔庙等。
我们的现场实拍视频将带您走进铝合金型材镀锌工角槽实体厂家大量现货产品的世界,让您亲眼见证其优点和特点,为您的购买决策提供有力支持。
以下是:铝合金型材镀锌工角槽实体厂家大量现货的图文介绍
双色铝型材生产过程中要注意的十个问题:(1)选择宽度、厚度适中的贴膜;由于铝型材加工断面形状复杂,外表向宽、窄悬殊较大,容易将飞边吹起,降低贴膜的遮盖能力,影响喷涂质量。贴膜过窄,则遮盖不住,显然不能喷涂。另一方面,在选择贴膜厚度时,只要能遮盖,具有弹性即可,不一定选择太厚的贴膜,因太厚的贴膜将增加铝型材加工生产成本,而且也没有必要。(2)贴膜后及时喷涂。型材贴膜以后,应及时进行喷涂,停放时间越短越好。如果停放时间太长,由于贴膜上的胶干燥,失去粘度,特则是经风一吹,贴膜脱落,导致喷涂同难。因此,为了确保贴膜及喷涂质量,一般贴膜以后的停放时间不要超过16h。(3)选样粘度适中的贴膜。在双色铝型材加工生产中,贴膜的合理选择是关键。贴膜的粘度过低则贴不住。贴膜容易脱落,给喷涂带来相当大的难度。贴膜的粘度过大,说明贴膜上的胶比较多,当贴膜撕掉后,容易将贴膜上的胶粘在型材上,影响型材的表面质量,另一方面,在选择贴膜时,尽可能选用胶的成分与涂漆成分一致或相接近,这样可减轻对漆膜色泽的影响。山东铝型网(4)确定颜色、分界面及分界线。铝型材加工在喷涂之前,一定要根据型材的使用功能以及客户的要求(合同要求),分清每个面所要喷徐的颜色,分界面是哪个面,分界线是哪条线,在什么位置:一般来说,内侧是浅色,外侧是深色在弄清了分界面、分界线及颜色的要求之后才能贴膜,要注意千万不能将膜的位置贴错。(5)贴膜质量:贴膜是双色铝型材加工加工中的一道关键工序,贴膜质量的好坏,直接影响到铝型材加工的表面质量,主要包括以下几个方画:一是贴膜时尽可能不要使贴膜形成过大的张力,也就足说不能使贴膜发生变形,否则贴好后的贴膜容易收缩,使铝型材加工两端出现无贴膜现象;另一方面,铝型材加工两端贴膜断开时,要用刀片切开,而不能拉断,否则,拉断的贴膜仍然要收缩;二是贴膜宽度要与贴面宽度相吻合,一般情况下,贴膜宽度稍大于铝型材加工的贴面宽度,若是贴膜过宽,超出铝型材加工边缘过多,当喷涂时,容易被压缩空气吹起,若是贴膜过窄,不能完全遮盖,显然是不行的;四是贴面分界线在沟槽边缘时,一定要将;贴膜的飞边压入沟槽内,否则,喷涂时气流容易将贴膜吹起,影响铝型材加工喷涂质量;五是贴膜时,一定将贴膜贴平,防止皱折、卷缩等现象;六是对于断面形状复杂的型材,如果一次贴膜困难时,可以分两次或多次贴膜,保证贴膜的覆盖质量;七是对一些壁厚较薄或悬臂较大等特殊断面的铝型材加工,贴膜时不能压得太紧,一定要注意不能使铝型材加工产生变形;八是 次喷涂后,铝型材加工的停放时间不能过长,否则会使型材表而落上灰尘,导致贴膜困难,从而影响贴膜质量:山东铝型材模具厂(6)严格执行贴膜工艺。铝型材加工贴膜必须经过 次喷涂后再贴,不允许型材铬化后直接贴膜,这是因为贴膜上有胶,如果直接将贴膜贴在铬化层上,胶就会粘在铬化层上,或者撕贴膜时,就会将铬化层,撕掉,这样就会大大降低漆膜的附着力,*终影响铝型材加工的喷涂质量,导致漆膜脱落,其后果不堪设想。(7)撕膜时间。铝型材加工经贴膜、喷涂以后,要撕去贴膜,但不能喷涂后马上就撕去贴膜,要控制好撕膜。-般来说,喷涂后经过流平,漆膜基本凝固,这一过程不能少于10min.然后才能撕去贴膜撕膜。否则,漆膜未开,撕膜的过程中容易将贴膜落在铝型材加工上,影响漆膜质量。另一方面,撕膜的时候动作要快,以免影响撕膜质量。(8)避免多次返工。在双色铝型材加工生产过程中,由于各种因素影响,返工是不可避免的,但是每返工一次就要增加一次固化。对漆膜来说。多次喷涂,漆膜厚度不断增加,再经多次固化,降低了漆膜附着力,容易造成漆膜脱落。因此,在双色铝型材加工的生产中尽可能避免多次返工。广东铝型材模具厂(9)膜厚的合理控制、双色铝型材加工生产是要经过两次以上的喷涂,如果我们还像单喷那样操作,就会导致有的面漆膜较厚,有的面漆膜较薄,从而引起膜厚严重不均匀。因此在喷涂时就要进行合理控制, 次喷徐时,只需对着面重点喷涂,而另一面可以不涂或少涂。第二次喷涂叫,闪样尽可能对需要的面重点喷,其他面不喷或少喷,同时还要根据 次喷涂情况以及选用的涂漆颜色.合理地控制第二次喷涂厚度,但必须保证第二次喷涂对前一次喷涂的浚盖效果。(10)喷涂顺序双色铝型材加工,需要涂上两种颜色,有两种颜色必然存在深色与浅色,喷涂必然有先有后,喷涂前必须要考虑哪种颜色先喷,哪种颜色后喷,要根据具体情况而定,若是先喷浅色、后喷深色,则先喷涂的浅色就要经过两次固化,即两次烘烤,容易将浅色烘烤变色,若是先喷深色、后喷浅色,则后喷浅色对前喷深色的覆盖性受到一定影响,要想覆盖深色就要增加漆膜厚度,但是漆膜厚到一定的程度后,又容易产生脱膜现象。因此。在实际生产中,采用先浅后深的工艺较为可行。
欢迎前来了解恒永兴金属材料销售 有限公司发布的 海南无缝钢管价格, 海南无缝钢管厂家信息,服务质量好,性价比高,为您节省采购成本!
说到船用铝板,大家*熟悉的要数5083铝板了。船用铝板是铝板产品研发应用的新兴领域,目前船板的生产能力已成为衡量铝板厂家综合实业的重要指标。那么,船舶制造厂家为何如此青睐5083铝板?5083铝板属于Al-Mg系合金,中等强度,具有耐蚀性好、焊接性优良、冷加工性较好的优势,广泛用于制造飞机油箱、油管、交通车辆、船舶钣金件、仪表、街灯支架、铆钉、五金制品、电器外壳等。在船舶制造领域,多采用5083H116/H321/H112状态的铝板,应用于船舶甲板、发动机台座、船侧、船底外板等部位。5083铝板满足船用铝板的选材要求:1、较高的比强度和比模量。船舶的结构强度和尺寸与材料的屈服强度和弹性模量密切相关,由于铝合金的弹性模量和密度大体相同,合金元素的添加也影响甚,因此在一定范围内提高屈服强度对减轻舰船结构有力。5083铝板属于中等强度,能同时具备优良的耐蚀性和可焊接性。2、焊接性优良。5083铝板具有良好的焊接抗裂性,在焊接时不容易出现裂纹现象。3、耐蚀性优良。耐蚀性能是船用合金的主要标志之一,5083铝板是典型的防锈铝板,耐腐性好,能适应恶劣的海洋环境,经久耐用。4、密度小。铝合金比重小,能减轻船板重量,节省能耗,增加载重。5、环保。铝合金不燃烧,遇火,而且回收利用率高,可循环再利用,环保性好。
通过温度控制提高挤压铝型材产量,通常,如果没有非预定的停机时间,那么*大产量主要决定于挤压速度,而后者受制于四个因素,其中三个固定不变而另一个则是可变的。 个因素是挤压机的挤压力,挤压力大的可在锭坯温度较低时顺利地挤压;第二个因素是模具设计,挤压时金属与模壁的摩擦通常可使通过的铝合金的温度上升35~62℃;第三个因素是被挤压合金的特性,是限制挤压速度的不可控制的因素,型材的出口温度一般不可超过540℃,否则,材料表面质量会下降,模痕明显加重,甚至出现粘铝、凹印、裂缝、撕裂等。*后一个因素是温度及其受控程度。如果铝型材挤压机的挤压力不够大,很难顺利挤压或甚至出现塞模现象而挤不动时,就可提高锭坯温度,但挤压速度应低些,以防材料的出口温度过高。每一个合金都有其特定的*优的挤压(锭坯)温度。生产实践证明,锭坯温度*好保持在430℃左右(挤压速度≥16mm/s时)。6063合金型材的出模温度不得超过500℃,6005合金的*高出口温度为512℃,6061合金的*好不大于525℃。出模温度的不大变化也会影响产品的产量与质量。挤压筒温度也是很重要的,特别应注意预热阶段的温度升高,应避免各层之间产生过大的热应力,*好是使挤压筒与衬套同时升高到工作温度。预热升温速度不得大于38℃/h。*好的预热规范是:升高到235℃,保温8h,继续升温到430℃,保温4h后,才投入工作。这样不但能保证内外温度均匀一致,而且有足够的时间一切内部热应力。当然在炉内加热挤压筒是*佳的预热方式。在挤压过程中,挤压筒温度应比锭坯温度低15~40℃。如果挤压速度过快,以致挤压筒温度上升到高于锭坯温度,就要设法使挤压筒温度下降,这不但是一件麻烦的工作,而且产量会下降。在生产速度上升过程中,有时受电偶控制的加热元件会被切断,可是挤压筒温度仍在上升。如果挤压筒温度高于470℃,挤压废品就会上升。应根据不同的合金确定理想的挤压筒温度。千万不要认为预热挤压筒是在浪费时间、消耗能源。某工厂为赶生产任务,一方面用内部电阻元件加热,另一方面又以液化气烧嘴加热。在这种情况,温度无法测量与控制,会产生巨大的热应力,内衬温度高,膨胀比外套的快,以致挤压筒裂开,并听到“炸裂”的声音。挤压轴在工作过程中会积蓄内应力,这种应力大到一定程度会产生疲劳裂纹,一旦受到非轴向的径向力作用就会断裂。因此,挤压轴的累计工作时间达到4500h后,*好进行一次应力处理,在430~480℃保温12h,然后随炉冷却到50℃以下。遗憾的是,我国很少有工厂照此处理。
生产优质表面建筑型材时,对挤压垫温度也应严格控制,以减少表面色调不一致废品量。固定挤压垫的质量比活动的好得多,能积聚更多的热量,因而能降低锭坯端头温度,能减少杂质进入型材内,有助于提高产量。美国卡斯图尔公司(Castool)采用压缩空气冷却挤压垫与挤压轴,使其温度降到50℃左右。模具温度对于获得高的产量起着重要的作用,一般不得低于430℃;另方面,也不得过高,否则,不但硬度可能下降,同时会产生氧化,主要在工作带。在模具加热过程中,应避免模具之间紧靠着,阻碍空气流通。*好采用带格的箱式加热炉,每个模放于一个单独的箱内。锭坯在挤压过程中的温度升高可达40℃左右或更高些,升高量主要决定于模具设计。为了获得*大产量,对各项温度决不可忽视,应记录各个温度并严加控制,以找出机台的*大产量与各项温度的关系。然后,铝型材挤压生产厂的员工都应牢记:温度的精密控制,对提高产量是至关重要的。
通过温度控制提高挤压铝型材产量,通常,如果没有非预定的停机时间,那么*大产量主要决定于挤压速度,而后者受制于四个因素,其中三个固定不变而另一个则是可变的。 个因素是挤压机的挤压力,挤压力大的可在锭坯温度较低时顺利地挤压;第二个因素是模具设计,挤压时金属与模壁的摩擦通常可使通过的铝合金的温度上升35~62℃;第三个因素是被挤压合金的特性,是限制挤压速度的不可控制的因素,型材的出口温度一般不可超过540℃,否则,材料表面质量会下降,模痕明显加重,甚至出现粘铝、凹印、裂缝、撕裂等。*后一个因素是温度及其受控程度。如果铝型材挤压机的挤压力不够大,很难顺利挤压或甚至出现塞模现象而挤不动时,就可提高锭坯温度,但挤压速度应低些,以防材料的出口温度过高。每一个合金都有其特定的*优的挤压(锭坯)温度。生产实践证明,锭坯温度*好保持在430℃左右(挤压速度≥16mm/s时)。6063合金型材的出模温度不得超过500℃,6005合金的*高出口温度为512℃,6061合金的*好不大于525℃。出模温度的不大变化也会影响产品的产量与质量。挤压筒温度也是很重要的,特别应注意预热阶段的温度升高,应避免各层之间产生过大的热应力,*好是使挤压筒与衬套同时升高到工作温度。预热升温速度不得大于38℃/h。*好的预热规范是:升高到235℃,保温8h,继续升温到430℃,保温4h后,才投入工作。这样不但能保证内外温度均匀一致,而且有足够的时间一切内部热应力。当然在炉内加热挤压筒是*佳的预热方式。在挤压过程中,挤压筒温度应比锭坯温度低15~40℃。如果挤压速度过快,以致挤压筒温度上升到高于锭坯温度,就要设法使挤压筒温度下降,这不但是一件麻烦的工作,而且产量会下降。在生产速度上升过程中,有时受电偶控制的加热元件会被切断,可是挤压筒温度仍在上升。如果挤压筒温度高于470℃,挤压废品就会上升。应根据不同的合金确定理想的挤压筒温度。千万不要认为预热挤压筒是在浪费时间、消耗能源。某工厂为赶生产任务,一方面用内部电阻元件加热,另一方面又以液化气烧嘴加热。在这种情况,温度无法测量与控制,会产生巨大的热应力,内衬温度高,膨胀比外套的快,以致挤压筒裂开,并听到“炸裂”的声音。挤压轴在工作过程中会积蓄内应力,这种应力大到一定程度会产生疲劳裂纹,一旦受到非轴向的径向力作用就会断裂。因此,挤压轴的累计工作时间达到4500h后,*好进行一次应力处理,在430~480℃保温12h,然后随炉冷却到50℃以下。遗憾的是,我国很少有工厂照此处理。
生产优质表面建筑型材时,对挤压垫温度也应严格控制,以减少表面色调不一致废品量。固定挤压垫的质量比活动的好得多,能积聚更多的热量,因而能降低锭坯端头温度,能减少杂质进入型材内,有助于提高产量。美国卡斯图尔公司(Castool)采用压缩空气冷却挤压垫与挤压轴,使其温度降到50℃左右。模具温度对于获得高的产量起着重要的作用,一般不得低于430℃;另方面,也不得过高,否则,不但硬度可能下降,同时会产生氧化,主要在工作带。在模具加热过程中,应避免模具之间紧靠着,阻碍空气流通。*好采用带格的箱式加热炉,每个模放于一个单独的箱内。锭坯在挤压过程中的温度升高可达40℃左右或更高些,升高量主要决定于模具设计。为了获得*大产量,对各项温度决不可忽视,应记录各个温度并严加控制,以找出机台的*大产量与各项温度的关系。然后,铝型材挤压生产厂的员工都应牢记:温度的精密控制,对提高产量是至关重要的。
铝及铝合金焊丝的选择主要根据母材的种类,对接头抗裂性能、力学性能及耐蚀性等方面的要求综合考虑。有时当某项成为主要矛盾时,则选择焊丝就着重从解决这个主要矛盾入手,兼顾其它方面要求。一般情况下,焊接铝及铝合金都采用与母材成分相同或相近牌号的焊丝,这样可以获得较好的耐蚀性;但焊接热裂倾向大的热处理强化铝合金时,选择焊丝主要从解决抗裂性入手,这时焊丝的成分与母材的差别就很大。
常见缺陷(焊接问题)及防止措施1、烧穿---产生原因:a、热输入量过大;b、坡口加工不当,焊件装配间隙过大;c、点固焊时焊点间距过大,焊接过程中产生较大的变形量。防止措施:a、适当减小焊接电流、电弧电压,提高焊接速度;b、大钝边尺寸,减小根部间隙;c、适当减小点固焊时焊点间距。2、气孔---产生原因:a、母材或焊丝上有油、锈、污、垢等;b、焊接场地空气流动大,不利于气体保护;c、焊接电弧过长,降低气体保护效果;d、喷嘴与工件距离过大,气体保护效果降低;e、焊接参数选择不当;f、重复起弧处产生气孔;g、保护气体纯度低,气体保护效果差;h、周围环境空气湿度大。防止措施:a、焊前仔细清理焊丝、焊件表面的油、污、锈、垢和氧化膜,采用含脱氧剂较高的焊丝;b、合理选择焊接场所;c、适当减小电弧长度;d、保持喷嘴与焊件之间的合理距离范围;e、尽量选择较粗的焊丝,同时增加工件坡口的钝边厚度,一方面可以允许使用大电流,公众号:焊王,另一方面也使焊缝金属中焊丝比例下降,这对降低气孔率是行之有效的;f、尽量不要在同一部位重复起弧,需要重复起弧时要对起弧处进行打磨或刮除;一道焊缝一旦起弧要尽量焊长些,不要随意断弧,以减少接头量,在接头处需要有一定焊缝重叠区;g、换保护气体;h、检查气流大小;i、预热母材;j、检查是否有漏气现象和气管损坏现象;k、在空气湿度较低时焊接,或采用加热系统。3、电弧不稳---产生原因:电源线连接、污物或者有风。防止措施:a、检查所有导电部分并使表面保持清洁;b、将接头处的脏物掉;c、尽量不要在能引起气流紊乱的地方进行焊接。4、焊缝成型差---产生原因:a、焊接规范选择不当;b、焊枪角度不正确;c、焊工操作不熟练;d、导电嘴孔径太大;e、焊丝、焊件及保护气体中含有水分。防止措施:a、反复调试选择合适的焊接规范;b、保持合适的焊枪倾角;c、选择合适的导电嘴孔径;d、焊前仔细清理焊丝、焊件,保证气体的纯度。5、未焊透---产生原因:a、焊接速度过快,电弧过长;b、坡口加工不当,装备间隙过小;c、焊接规范过小;d、焊接电流不稳定。防止措施:a、适当减慢焊接速度,压低电弧;b、适当减小钝边或增加根部间隙;c、增加焊接电流及电弧电压,保证母材足够的热输入能量;d、增加稳压电源装置e、细焊丝有助于提高熔深,粗焊丝提高熔敷量,应酌情选择。6、未熔合---产生原因:a、焊接部位氧化膜或锈迹未干净;b、热输入不足。防止措施:a、焊前清理待焊处表面b、提高焊接电流、电弧电压,减小焊接速度;c、对于厚板采用U型接头,而一般不采用V型接头。7、裂纹---产生原因:a、结构设计不合理,焊缝过于集中,造成焊接接头拘束应力过大b、熔池过大、过热、合金元素烧损多;c、焊缝末端的弧坑冷却快;d、焊丝成分与母材不匹配;e、焊缝深宽比过大。防止措施:a、正确设计焊接结构,合理布置焊缝,使焊缝尽量避开应力集中区,合理选择焊接顺序;b、减小焊接电流或适当增加焊接速度;c、收弧操作要正确,加入引弧板或采用电流衰减装置填满弧坑;d、正确选用焊丝。8、夹渣---产生原因:a、焊前清理不彻底;b、焊接电流过大,导致导电嘴局部熔化混入熔池而形成夹渣c、焊接速度过快。防止措施:a、加强焊前清理工作,多道焊时,每焊完一道同样要进行焊缝清理;b、在保证熔透的情况下,适当减小焊接电流,大电流焊接时导电嘴不要压太低;c、适当降低焊接速度,采用含脱氧剂较高的焊丝,提高电弧电压。9、咬边---产生原因:a、焊接电流太大,焊接电压太高;b、焊接速度过快,填丝太少;c、焊枪摆动不均匀。防止措施:a、适当的调整焊接电流和电弧电压;b、适当增加送丝速度或降低焊接速度;c、力求焊枪摆动均匀。10、焊缝污染---产生原因:a、不适当的保护气体覆盖;b、焊丝不洁;c、母材不洁。防止措施:a、检查送气软管是否有泄漏情况,是否有抽风,气嘴是否松动,保护气体使用是否正确;b、是否正确的储存焊接材料;c、在使用其它的机械清理前,先将油和油脂类物质掉;d、在使用不锈钢刷之前将氧化物掉。11、送丝性不良---产生原因:A、导电嘴与焊丝打火;b、焊丝磨损、喷弧;d、送丝软管太长或太紧;e、送丝轮不适当或磨损;f、焊接材料表面毛刺、划伤、灰尘和污物较多。防止措施:a、降低送丝轮张力,使用慢启动系统;b、检查所有焊丝接触表面情况并尽量减少金属与金属的接触面;c、检查导电嘴情况及送丝软管情况,检查送丝轮状况;d、检查导电嘴的直径大小是否匹配;e、使用耐磨材料以避免送丝过程中发生截断情况;f、检查焊丝盘磨损状况;g、选择合适的送丝轮尺寸,形状及合适的表面情况;h、选择表面质量较好的焊接材料。12、起弧不良---产生原因:a、接地不良;b、导电嘴尺寸不对;c、没有保护气体。防止措施:a、检查所有接地情况是否良好,使用慢启动或热起弧方式以方便起弧;b、检查导电嘴内空是否被金属材料堵塞;c、使用气体预清理功能;d、改变焊接参数。
常见缺陷(焊接问题)及防止措施1、烧穿---产生原因:a、热输入量过大;b、坡口加工不当,焊件装配间隙过大;c、点固焊时焊点间距过大,焊接过程中产生较大的变形量。防止措施:a、适当减小焊接电流、电弧电压,提高焊接速度;b、大钝边尺寸,减小根部间隙;c、适当减小点固焊时焊点间距。2、气孔---产生原因:a、母材或焊丝上有油、锈、污、垢等;b、焊接场地空气流动大,不利于气体保护;c、焊接电弧过长,降低气体保护效果;d、喷嘴与工件距离过大,气体保护效果降低;e、焊接参数选择不当;f、重复起弧处产生气孔;g、保护气体纯度低,气体保护效果差;h、周围环境空气湿度大。防止措施:a、焊前仔细清理焊丝、焊件表面的油、污、锈、垢和氧化膜,采用含脱氧剂较高的焊丝;b、合理选择焊接场所;c、适当减小电弧长度;d、保持喷嘴与焊件之间的合理距离范围;e、尽量选择较粗的焊丝,同时增加工件坡口的钝边厚度,一方面可以允许使用大电流,公众号:焊王,另一方面也使焊缝金属中焊丝比例下降,这对降低气孔率是行之有效的;f、尽量不要在同一部位重复起弧,需要重复起弧时要对起弧处进行打磨或刮除;一道焊缝一旦起弧要尽量焊长些,不要随意断弧,以减少接头量,在接头处需要有一定焊缝重叠区;g、换保护气体;h、检查气流大小;i、预热母材;j、检查是否有漏气现象和气管损坏现象;k、在空气湿度较低时焊接,或采用加热系统。3、电弧不稳---产生原因:电源线连接、污物或者有风。防止措施:a、检查所有导电部分并使表面保持清洁;b、将接头处的脏物掉;c、尽量不要在能引起气流紊乱的地方进行焊接。4、焊缝成型差---产生原因:a、焊接规范选择不当;b、焊枪角度不正确;c、焊工操作不熟练;d、导电嘴孔径太大;e、焊丝、焊件及保护气体中含有水分。防止措施:a、反复调试选择合适的焊接规范;b、保持合适的焊枪倾角;c、选择合适的导电嘴孔径;d、焊前仔细清理焊丝、焊件,保证气体的纯度。5、未焊透---产生原因:a、焊接速度过快,电弧过长;b、坡口加工不当,装备间隙过小;c、焊接规范过小;d、焊接电流不稳定。防止措施:a、适当减慢焊接速度,压低电弧;b、适当减小钝边或增加根部间隙;c、增加焊接电流及电弧电压,保证母材足够的热输入能量;d、增加稳压电源装置e、细焊丝有助于提高熔深,粗焊丝提高熔敷量,应酌情选择。6、未熔合---产生原因:a、焊接部位氧化膜或锈迹未干净;b、热输入不足。防止措施:a、焊前清理待焊处表面b、提高焊接电流、电弧电压,减小焊接速度;c、对于厚板采用U型接头,而一般不采用V型接头。7、裂纹---产生原因:a、结构设计不合理,焊缝过于集中,造成焊接接头拘束应力过大b、熔池过大、过热、合金元素烧损多;c、焊缝末端的弧坑冷却快;d、焊丝成分与母材不匹配;e、焊缝深宽比过大。防止措施:a、正确设计焊接结构,合理布置焊缝,使焊缝尽量避开应力集中区,合理选择焊接顺序;b、减小焊接电流或适当增加焊接速度;c、收弧操作要正确,加入引弧板或采用电流衰减装置填满弧坑;d、正确选用焊丝。8、夹渣---产生原因:a、焊前清理不彻底;b、焊接电流过大,导致导电嘴局部熔化混入熔池而形成夹渣c、焊接速度过快。防止措施:a、加强焊前清理工作,多道焊时,每焊完一道同样要进行焊缝清理;b、在保证熔透的情况下,适当减小焊接电流,大电流焊接时导电嘴不要压太低;c、适当降低焊接速度,采用含脱氧剂较高的焊丝,提高电弧电压。9、咬边---产生原因:a、焊接电流太大,焊接电压太高;b、焊接速度过快,填丝太少;c、焊枪摆动不均匀。防止措施:a、适当的调整焊接电流和电弧电压;b、适当增加送丝速度或降低焊接速度;c、力求焊枪摆动均匀。10、焊缝污染---产生原因:a、不适当的保护气体覆盖;b、焊丝不洁;c、母材不洁。防止措施:a、检查送气软管是否有泄漏情况,是否有抽风,气嘴是否松动,保护气体使用是否正确;b、是否正确的储存焊接材料;c、在使用其它的机械清理前,先将油和油脂类物质掉;d、在使用不锈钢刷之前将氧化物掉。11、送丝性不良---产生原因:A、导电嘴与焊丝打火;b、焊丝磨损、喷弧;d、送丝软管太长或太紧;e、送丝轮不适当或磨损;f、焊接材料表面毛刺、划伤、灰尘和污物较多。防止措施:a、降低送丝轮张力,使用慢启动系统;b、检查所有焊丝接触表面情况并尽量减少金属与金属的接触面;c、检查导电嘴情况及送丝软管情况,检查送丝轮状况;d、检查导电嘴的直径大小是否匹配;e、使用耐磨材料以避免送丝过程中发生截断情况;f、检查焊丝盘磨损状况;g、选择合适的送丝轮尺寸,形状及合适的表面情况;h、选择表面质量较好的焊接材料。12、起弧不良---产生原因:a、接地不良;b、导电嘴尺寸不对;c、没有保护气体。防止措施:a、检查所有接地情况是否良好,使用慢启动或热起弧方式以方便起弧;b、检查导电嘴内空是否被金属材料堵塞;c、使用气体预清理功能;d、改变焊接参数。
铝型材散热器生产工艺:首先贴膜不能直接贴在铬化层上,否则会影响膜的附着力;其次,贴膜后要及时喷涂不能停放时间过长,否则容易导致贴膜脱落,严重时还要重新贴膜;再次是撕膜时要控制流平时间,不能贴膜后马上撕膜,这样会对产品质量带来一定的影响;*后是两种颜色的喷涂顺序要根据具体情况确定,既要考虑到两次固化,又要考虑到遮盖效果。贴膜质量控制:散热器铝型材质量控制中贴膜质量很重要,若贴不好,会导致喷涂困难,如贴膜的张力不大、压紧程度要控制好;对形状复杂的部位要分开贴膜,贴膜后要检查贴膜是否贴牢。否则将会给喷涂带来麻烦。影响喷涂质量。公司生产的铝型材产品均由专业的技术人员严格把关,并拥有专业的生产设备,保证质量问题,客户可放心选购我厂产品。铝型材散热器的贴膜材质:首先要对贴膜材质合理选择,根据散热器铝型材产品的要求、表面处理方式,选择相应的贴膜,同是还要考虑贴膜上的胶对铝型材表面质量的影响。
缩孔是铝合金压铸件常见的内部缺陷,常出现在产品壁厚较大或者易形成热点的位置。一般来讲,只要缩孔不影响产品的使用性能,都以合格的方式来判定。然而,对于一些重要部位,如汽车发动机汽缸体的冷却水道孔或润滑油道孔,出现缩孔是不允许判定合格的。
某企业的一款铝合金制发动机曲轴箱,采用布勒28000kN冷室压铸机铸造,材质为ADC12合金,成分见表1。铸件毛坯质量为6.3 kg,后工序进行X射线探伤时发现第二个曲轴轴承孔油道出现缩孔,离油道约8 mm,存在较大的漏油风险。据统计,2017年该位置的缩孔报废率为5%,经过一系列的探索,成功地将废品率降低为0.2%。本课题从铝合金压铸件缩孔的形成机理[1-5]和铸造条件两方面出发,分析铸件产生缩孔的原因,寻求改善措施,以期为日后解决铝合金压铸件缩孔问题提供参考。一、铝合金压铸件缩孔形成机理及形态--缩孔形成机理:导致铝合金压铸件缩孔的原因较多,追溯其本源,主要是铝合金从液相向固相转变过程中铝液补缩不足而导致。常见的缩孔原因有:①模温梯度不合理,导致铝液局部收缩不一致。②铝液浇注量偏少,导致料饼薄,增压阶段补压不足。③模具存在热结或尖锐区域。④模具的内浇口宽度不够,面积较小,导致铸件过早凝固,增压阶段压力传递受阻、铝液无法补缩。⑤铸造压力设置过低,补缩效果较差。图1为铝合金铸件缩孔形成的示意图。铸件缩孔形态:缩孔是一种铝合金压铸件乃至铸件常见的内部缺陷,常出现在产品壁厚较大、模具尖角和模温温差较大等区域。图2为某款发动机曲轴箱缩孔形态,缩孔呈似椭圆状,距离轴承油道孔约10 mm,内壁粗糙,无光泽。缩孔区域铸件壁厚较大,约为22 mm;油道孔销子前端无冷却水,模温较高。汽车发动机曲轴的两大轴颈(主轴颈和连杆轴颈)工作载荷较大,磨损严重,工作时必须进行压力润滑。在此情况下,轴颈的油道孔附近若存在缩孔,将会严重影响润滑效果。二、缩孔相关对策:铝合金压铸件产生铸造缺陷的原因有产品本身的结构特征、模具设计得浇注系统及冷却系统设计不合理、工艺参数设计不合理等原因[1~4]。根据常见的铸造缺陷原因以及铝合金铸件缺陷处理流程,探索解决铝合金压铸件厚大部位缩孔的相应对策。前期分析及对策:铸件缩孔的前期分析从容易操作的工艺参数出发,通过现场测量及观察,测得模具内浇口厚度为4 mm,计算的内浇口速度为40 m/s,产品壁厚*薄处为4.6 mm;料饼厚度为25 mm;铸造压力为60MPa。由经验可知,模具设计符合产品的结构特征,模具浇注系统应该不存在增压阶段补缩不足的问题。但是,增压阶段的铝液补缩与料饼厚度和增压压力有直接的关系,合适的料饼厚度与铸造压力才能形成内部组 织致密的铸件,因此,可以怀疑缩孔是由铸造压力偏低和料饼偏薄而导致的。前期铸件缩孔的对策分为两个:①铸造压力由之前的65MPa提高至90MPa;②料饼厚度有原来的25 mm调整为30 mm。采用上述措施后,经过小批量专流验证,缩孔率由5%减低为4.8%,效果不明显,说明工艺参数不是引起铸件缩孔的主因。中期分析及对策:由于引起铸件缩孔的本质原因是铝液凝固时补缩不足而导致,而模具温度分布不均容易导致铝液凝固顺序不合理,从而补缩不足,因此,中期对策分析主要从确保合理的模具温度入手。由产品3D模型可知,铸件缩孔处壁厚为22.6mm,壁厚较大,容易引起较高的模具温度。铝液凝固时,壁厚较大铸件内部铝液由于温度较高,尚处于液相或者固液混合相,而此时内浇口进行补缩的通道可能已经凝固。这样,在增压阶段铸件无法进行铝液补缩,从而有形成缩孔的可能。为确保合适的模具温度,采用热成像仪测得脱模剂喷涂后模具*高温度为272℃(见图3),高于正常的模具喷涂后温度,其他区域模具温度及其分布整体正常。因此,需要降低缩孔处模温。另外,测得此处冷却水孔底部距离模具型腔表面距离较大为20 mm,因为较大的热传递距离会降低模具的冷却效果,所以需要对冷却水孔进行更改。为降低缩孔处模具温度,主要采取3个方法:①改善模具冷却系统。将缩孔附件的冷却水孔深度加深,由距模具表面20 mm变成12 mm,以此快速带走附近模具热量,降低模温;将所有模具冷却水管与水管统一编号,一一对应,防止模具保全时装错,影响冷却效果[5,6]。②降低浇注温度,由675℃变为645℃。③延长缩孔处模具喷涂时间,由2 s变成3 s。实施上述整改措施后,缩孔区域模具喷涂后温度大幅度降低,约为200℃,属于正常范围。缩孔率有4.8%降低到4%,说明此类措施对缩孔具有一定效果,但不能彻底解决此区域的缩孔问题。后期分析及对策:通过前面两次改善,基本保证压铸模具处于理论上的合理状态,即浇注系统设计合理、冷却系统布置合适,工艺参数设计*优。然而,铸件缩孔率仍有4%之多。铸件缩孔处壁厚为22.6 mm,远大于其他部位的壁厚,较大的壁厚可能引起铸件中心凝固时补缩不足,增压结束后此区域还没有完全凝固,继续收缩产生缩孔[7~10],模流分析见图4。因此,如何解决铸件缩孔处的补缩不足,也许才是问题的关键。一般来讲,铸件的补缩时通过料饼→浇道→内浇口→铸件这条路径进行的。由于铸件厚大部位后于内浇口凝固,切断了增压后期的补缩通道,因此无法补缩。
缩孔是铝合金压铸件常见的内部缺陷,常出现在产品壁厚较大或者易形成热点的位置。一般来讲,只要缩孔不影响产品的使用性能,都以合格的方式来判定。然而,对于一些重要部位,如汽车发动机汽缸体的冷却水道孔或润滑油道孔,出现缩孔是不允许判定合格的。
某企业的一款铝合金制发动机曲轴箱,采用布勒28000kN冷室压铸机铸造,材质为ADC12合金,成分见表1。铸件毛坯质量为6.3 kg,后工序进行X射线探伤时发现第二个曲轴轴承孔油道出现缩孔,离油道约8 mm,存在较大的漏油风险。据统计,2017年该位置的缩孔报废率为5%,经过一系列的探索,成功地将废品率降低为0.2%。本课题从铝合金压铸件缩孔的形成机理[1-5]和铸造条件两方面出发,分析铸件产生缩孔的原因,寻求改善措施,以期为日后解决铝合金压铸件缩孔问题提供参考。一、铝合金压铸件缩孔形成机理及形态--缩孔形成机理:导致铝合金压铸件缩孔的原因较多,追溯其本源,主要是铝合金从液相向固相转变过程中铝液补缩不足而导致。常见的缩孔原因有:①模温梯度不合理,导致铝液局部收缩不一致。②铝液浇注量偏少,导致料饼薄,增压阶段补压不足。③模具存在热结或尖锐区域。④模具的内浇口宽度不够,面积较小,导致铸件过早凝固,增压阶段压力传递受阻、铝液无法补缩。⑤铸造压力设置过低,补缩效果较差。图1为铝合金铸件缩孔形成的示意图。铸件缩孔形态:缩孔是一种铝合金压铸件乃至铸件常见的内部缺陷,常出现在产品壁厚较大、模具尖角和模温温差较大等区域。图2为某款发动机曲轴箱缩孔形态,缩孔呈似椭圆状,距离轴承油道孔约10 mm,内壁粗糙,无光泽。缩孔区域铸件壁厚较大,约为22 mm;油道孔销子前端无冷却水,模温较高。汽车发动机曲轴的两大轴颈(主轴颈和连杆轴颈)工作载荷较大,磨损严重,工作时必须进行压力润滑。在此情况下,轴颈的油道孔附近若存在缩孔,将会严重影响润滑效果。二、缩孔相关对策:铝合金压铸件产生铸造缺陷的原因有产品本身的结构特征、模具设计得浇注系统及冷却系统设计不合理、工艺参数设计不合理等原因[1~4]。根据常见的铸造缺陷原因以及铝合金铸件缺陷处理流程,探索解决铝合金压铸件厚大部位缩孔的相应对策。前期分析及对策:铸件缩孔的前期分析从容易操作的工艺参数出发,通过现场测量及观察,测得模具内浇口厚度为4 mm,计算的内浇口速度为40 m/s,产品壁厚*薄处为4.6 mm;料饼厚度为25 mm;铸造压力为60MPa。由经验可知,模具设计符合产品的结构特征,模具浇注系统应该不存在增压阶段补缩不足的问题。但是,增压阶段的铝液补缩与料饼厚度和增压压力有直接的关系,合适的料饼厚度与铸造压力才能形成内部组 织致密的铸件,因此,可以怀疑缩孔是由铸造压力偏低和料饼偏薄而导致的。前期铸件缩孔的对策分为两个:①铸造压力由之前的65MPa提高至90MPa;②料饼厚度有原来的25 mm调整为30 mm。采用上述措施后,经过小批量专流验证,缩孔率由5%减低为4.8%,效果不明显,说明工艺参数不是引起铸件缩孔的主因。中期分析及对策:由于引起铸件缩孔的本质原因是铝液凝固时补缩不足而导致,而模具温度分布不均容易导致铝液凝固顺序不合理,从而补缩不足,因此,中期对策分析主要从确保合理的模具温度入手。由产品3D模型可知,铸件缩孔处壁厚为22.6mm,壁厚较大,容易引起较高的模具温度。铝液凝固时,壁厚较大铸件内部铝液由于温度较高,尚处于液相或者固液混合相,而此时内浇口进行补缩的通道可能已经凝固。这样,在增压阶段铸件无法进行铝液补缩,从而有形成缩孔的可能。为确保合适的模具温度,采用热成像仪测得脱模剂喷涂后模具*高温度为272℃(见图3),高于正常的模具喷涂后温度,其他区域模具温度及其分布整体正常。因此,需要降低缩孔处模温。另外,测得此处冷却水孔底部距离模具型腔表面距离较大为20 mm,因为较大的热传递距离会降低模具的冷却效果,所以需要对冷却水孔进行更改。为降低缩孔处模具温度,主要采取3个方法:①改善模具冷却系统。将缩孔附件的冷却水孔深度加深,由距模具表面20 mm变成12 mm,以此快速带走附近模具热量,降低模温;将所有模具冷却水管与水管统一编号,一一对应,防止模具保全时装错,影响冷却效果[5,6]。②降低浇注温度,由675℃变为645℃。③延长缩孔处模具喷涂时间,由2 s变成3 s。实施上述整改措施后,缩孔区域模具喷涂后温度大幅度降低,约为200℃,属于正常范围。缩孔率有4.8%降低到4%,说明此类措施对缩孔具有一定效果,但不能彻底解决此区域的缩孔问题。后期分析及对策:通过前面两次改善,基本保证压铸模具处于理论上的合理状态,即浇注系统设计合理、冷却系统布置合适,工艺参数设计*优。然而,铸件缩孔率仍有4%之多。铸件缩孔处壁厚为22.6 mm,远大于其他部位的壁厚,较大的壁厚可能引起铸件中心凝固时补缩不足,增压结束后此区域还没有完全凝固,继续收缩产生缩孔[7~10],模流分析见图4。因此,如何解决铸件缩孔处的补缩不足,也许才是问题的关键。一般来讲,铸件的补缩时通过料饼→浇道→内浇口→铸件这条路径进行的。由于铸件厚大部位后于内浇口凝固,切断了增压后期的补缩通道,因此无法补缩。
选购铝合金型材镀锌工角槽实体厂家大量现货来海南省找恒永兴金属材料销售
有限公司,我们是厂家直销,产品型号齐全,确保您购买的每一件产品都符合高标准的质量要求,选择我们就是选择品质与服务的双重保障。联系人:李经理-18802286588,{QQ:554918566},地址:[北辰区双街镇京津路西(北方实业发展有限公司内)]。